Reactor Relay 4-Channel 20-Amp with USB Interface
LRR420_USB
Reactor Relay
The LRR420_USB can be configured to will allow attached sensors to trigger relays at a predetermined setting. 0 to 5 volt sensors can be connected to the board which will convert the voltage to a numerical value between 0 and 255. You can set what value you want the relays to trigger! Trigger above, below or in between values. Set delays after the value has been reached (light stays on for 10 minutes after sensor activation). Options are limitless!USB Configuration
The TLR420_USB Reactor Relay uses a USB cable to connect to your computer to configure the board. Remember, once the board is configured, the computer is no longer needed. Making this the ideal choice for controlling relays using a sensor or contact closure!
Reactor Relay 4-Channel 20-Amp with USB Interface
LRR420_USB- OVERVIEW
- USB Interface
- Reactor Setup
- Board Features
- Power & More
- Relay Logic
- ACCESSORIES
- Data Sheets
Reactor Relay at a Glance
- 4 20-Amp Relay Installed
- Single Pole Double Throw (SPDT) Relay
- Normally Open 20-amps, Normally Closed 10-amps
- Wire Using 1/4" Quick Disconnect Terminal
- Temperature Rating -40° C to 85° C
- Not-Expandable - Onboard USB Interface Module
- Configure Board with USB Connection
- Plugs Directly into USB Port
- Configure Using Base Station - Configuration options
- 256 Different Trigger Points
- 8 Background Timers Available
- 4 Rotation Counters Available
- Configure Activation Sequences
Operates Without a Computer
Once configured the board will operate on it's own and no computer is needed!
Reactor Relay
USB Configuration
The LRR420_USB Reactor Controller must be configured using a computer and the included Base Station Software. Once configured, a Reactor will operate without a computer. By choosing a USB version you will connect your computer to your controller via a USB cable. This is the easiest and most popular way to connect to the Reactor Board. At any time, a computer may monitor the Reactor, Trigger Events, Activate Relays, or Change Configuration settings. A computer can take over a Reactor or a Reactor can operate autonomously (without a computer).Inputs Monitored
Once a Reactor is configured, the Reactor monitors inputs. When inputs reach user-defined limits, relays can turn on or off. Reactors allow much more than simple relay control. Reactor inputs can trigger timers and rotations. A timer allows a relay to activate over a duration of time. A rotation is a simple counter, in which relays can be assigned to each "count". This allows powerful functions such as relay activation sequencing, flashing, and stepping. Event Piping allows timers and rotations to trigger other timers and rotations. This is very powerful for setting up complex relay activation sequences.Mounts as a COM Port
This ProXR series controller connects to the USB port of your computer and will mount as a COM port on your PC. USB Drivers will most likely be needed and can be found in the resources section to the right and will also be available in the Base Station Software. Windows 7 & 8 users will automatically download and install the necessary drivers.ZUSB Modules

8 Inputs Available
Reactor Inputs play a vital role in the use of a Reactor controller. Analog inputs are simply inputs that are sensitive to voltages. Analog Inputs are capable of reading switches and sensors operating in the 0 to 5VDC range. Once configured, the Reactor CPU is constantly monitoring external sensors using 8 analog inputs that can read switches, resistance changes, or voltages from 0 to 5VDC. Inputs can be configured to trigger relays, relay timers and relay activation sequences.Input Voltage Changes
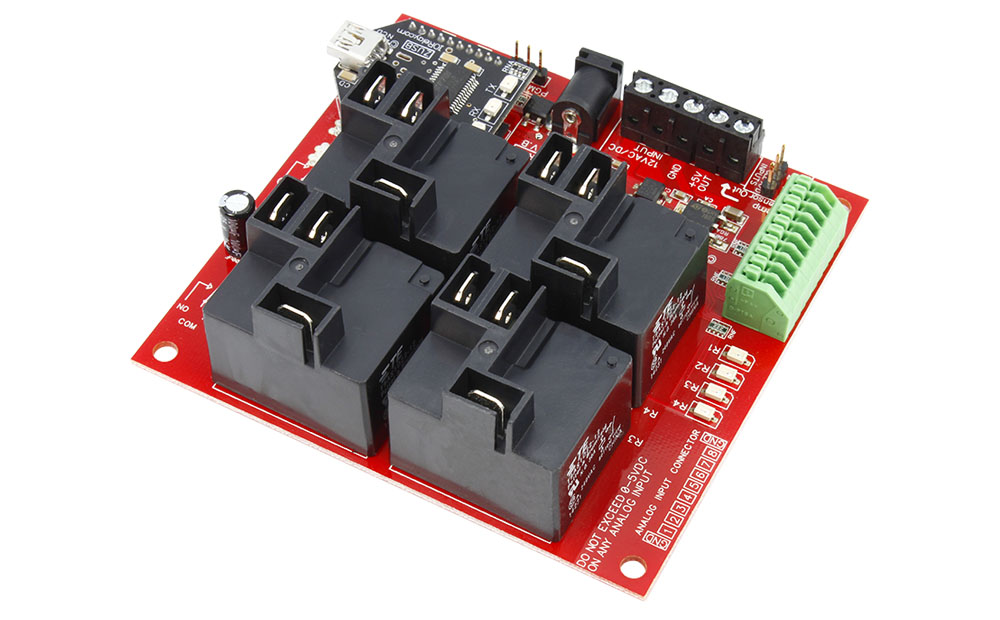
- For Example
- A voltage input of 0 Volts is interpreted as a value of 0
- A voltage input of 2.5 Volts is interpreted as a value of 128
- A voltage input of 5 Volts is interpreted as a value of 255
So if you divide 5 Volts by 256 possible steps (0-255 for 8-Bit resolution), the Reactor controller is sensitive to voltage changes as small as 0.0195 Volts. A Reactor controller has 8 inputs. Each input is capable of reading a separate voltage from 0 to 5 VDC, provided all voltages can share a common ground. You configure exactly what value you want the board to trigger the relay or start a sequence or delay!
Who’s Qualified to Use the Reactor Series?
Some computer skills required. The Reactor Relays do not require programming, simply configure the device with the included Base Station Software. While programming is not required and simple functions can be done rather easily with basic computer skills, complex events can be configured which will require some understanding and patience.Induction Capacitors

Base Station Configuration
Reactor boards are configured using the Free Base Station Software. The GUI interface makes it easy to configure simple automation tasks with a point and click interface! Download Base Station
Base Station Reactor Configuration
Base Station Software
Base Station will assist you in learning how this device functions and is the ultimate reference tool for configuring, testing and controlling this device. Base Station software supports every feature of this device - no other controller manufacturer even comes close to offering this type of software. Base Station works by communicating with your controller to identify the model and provides the appropriate graphical user interface for setting up and testing the identified device. All Reactor configurations will be made through Base Station and an overview will be discussed below. To help you get started and learn this controller Quick Start Guides are available for just about every feature. As you discover a feature in Base Station a link is provided where you can easily download the Quick Start Guide. Download Base StationeConfigure Each Input
The Reactor Relay allows users to define the activation of a relay or an event based on the voltage readings of the analog inputs. An input can trigger a relay directly or an input can trigger an
Using Input Values

Reading from Left to right, the settings above indicate Input 1 will trigger a relay when Analog Input 1 is above 200. We have defined that a relay will turn on when the input level is defined by a value of 200.

In the above example, a relay is triggered when an analog input is inside a set range between 100 and 202. By defining two limits, you can further narrow the parameters for the activation of a relay. The limits can also be assigned to set the relay to be activated outside two set limits.
Output Configuration

There are many ways to directly control a relay from an input. Relays 1-5 in the below example shows how inputs can turn relays on, off, toggle relay state, set the relay to match the state of the input, or set the relay to NOT equal the state of a input.
In the example below, Relay 6 is controlled by Timer 1. In other words, if Timer 1 is active, the relay will stay ON. Otherwise, the relay will turn off. This is a great way to activate a light for a given period of time. If you are interested in Time Delay Relay, timers will be discussed on our Time Delay Relay Page.
Complex Automation through Experimentation
Dont be afraid to experiment with Reactor! Some complex automation can be achieved by experimenting with Reactor settings. Of course Reactor is capable of triggering relays and it can also trigger events. Relays can be associated with events, allowing you to play with all kinds of complex timing and counting settings. Events greatly expand the pallet of functionality available to Reactor.Computer Controlled Relays
Software developers who need remote access to a Reactor controller will find themselves at home.  The Reactor supports a very powerful computer-based command set, so it is possible for a computer to operate the relays and read sensor inputs.  The computer can over-ride the Reactor decision logic, trigger events, and return control of the relays back to the Reactor Logic. Configuration settings are stored in files that can be loaded into other Reactor controllers.Many More Options
We have just touched on the many ways the Reactor board can be configured. The applications that this board can be use in are extensive. For a more detailed look at the configuration and setup you can look at the Reactor Series Quick Start Guide.Reactor Video
Attention: 0 - 5 Volt DC Input Only
Please Note: Analog inputs can accept voltages from 0 to 5VDC ONLY. Higher voltages and negative voltages will damage the Reactor controller. Improper use of these inputs can cause irreparable damage to the board.
Reactor Board Features
Reactor Relay
In this tab we'll take a look at the Reactor board design itself. The Reactor series controllers are machine manufactured for a highly accurate and reliable design. Fully tested before they leave the production facility each Reactor controller is ready to stand up to rigorous demands from heat, cold or vibration. The best test of all is the numerous boards in the field from customers all over the world in all sorts of conditions. Take it from us, these controllers will hold up!Essential Power Requirements
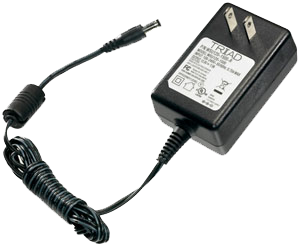
Amperage Rating
The 20-Amp relay is reated for 20-amps on the Normally Open connection and rated for 10-amps on the Normally Closed connection. Please keep this in mind when wiring to the Normally Closed side it is only rated for 10-amps.20-Amp SPDT Relay Installed
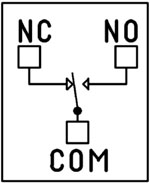
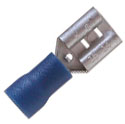
2-Million Cycles
Reactor series boardss are designed for long life, you should expect to get years of service from your controller and literally 2-million cycles from the relays on board. With a 5-year warranty and a money back guarantee you have nothing to loose!This Board is RoHS Compliant
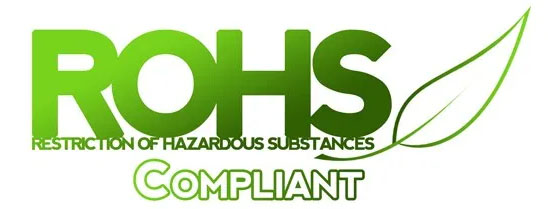
Not Expandable
The Reactor Series controllers are not expandable.Break-A-Way Tabs for a Smaller Design
The Reactor relays have a great feature where space is a premium - Break-A-Way Tabs. The Break-A-Way Tabs allow most boards to fit in an optional undrilled plastic enclosure. Snap off the Break-A-Way Tabs and you have a controller with a smaller profile when you need to fit in a tight space.30-Day Warranty/Money Back Guarantee
Reactor series controllers are guaranteed against manufacturing and functionality defects for a full 30 days! Not to mention a 30-day money back guarantee! If for any reason you are not happy with a relay purchased from Relay Pros, simply return it within 30 days and we will give you your money back! Controllers that are damaged by our customers will not of course be warranted under any circumstances.Shipping
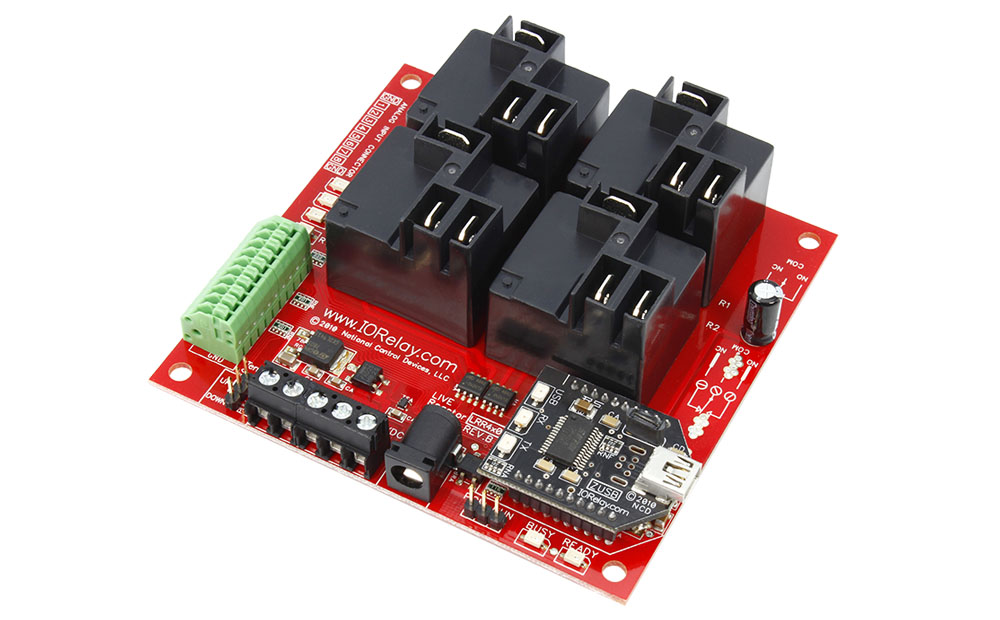
Sensor Control Is Here!
Trigger relays with a sensor with and configure with included Base Station software. Here's a lists of great features:- User Friendly Software
- Point & Click Interface - No Programming Knowledge Required
- Override Sensor When Computer is Connected to Board
- Read Sensor Levels in Base Station
- Read Status of Relays in Base Station
- User Friendly Board Design
- 8 Analog Sensor Inputs Available (0 to 5 Volt Only)
- Break-A-Way Tabs lets you decide the board's size
- Direct relay connections make connecting to the relays easy
Building a Power Budget
The operating range of the board is between 9 & 14 VDC, any power outside this range and the board can become unreliable. Use the tables below to build a power budget for the board you have based on the module you have and the anticipated time the relay will be active.
Power & More
20/30 Amp Relay Board Specifications
This table covers all NCD boards with 20 or 30 amp relays installed. All ratings assume 12VDC operation at 70°F (21°C). Please note that most ratings are estimated and may be subject to periodic revision. Some ratings represent stock controller settings without performance enhancement optimizations. The estimated processing time can be impacted by background services and choice of commands. Standby power consumption assume no communications module is installed and no relays are active on the controller. Please add the power consumption of the activated relays and communications module to obtain a better estimation of power consumption.Specs of NCD SPDT Relay Boards | Minimum | Nominal | Maximum | Notes |
Operational Voltages | 10VDC | 12VDC | 15VDC | |
Standby Power Consumption | 35mA | 100mA | 200mA | No Active Relays, No Com Module |
Relay Power Consumption | 28mA | 35mA | 60mA | Consumption of Each Activated Relay |
Operational Temperature Range | -40°F (-40°C) | 70°F (21°C) | 185°F (85°C) | Theoretical Component Limits Shown |
Storage Temperature Range | -67°F (-55°C) | 70°F (21°C) | 185°F (85°C) |
Theoretical Component Limits Shown |
Operational Ambient Air Humidity | 0% | 50% | 70% | Non-Condensing Humidity Values Shown |
Relay Activation Time | 15ms | Needs Further Validation | ||
Relay Deactivation Time | 10mS | Needs Further Validation | ||
Operational Life Mechanical | 10,000,000 | Component Operation Rating | ||
Operational Life Electrical | 100,000 | Component Rating at Maximum Load |
Communication Module Specifications
This table covers all NCD Communication Modules. While NCD communication modules operate at 3.3VDC, the ratings below highlight the effect they will have on the master controller operating at 12VDC at 70°F (21°C). Maximum ratings should be used for power budget planning purposes and may reflect short term absolute maximum peak current consumption. Some ratings are estimated and subject to periodic revision.Specs of NCD Communication Modules | Minimum | Nominal | Maximum | Notes |
Operational Temperature Range | -40°F (-40°C) | 70°F (21°C) | 185°F (85°C) | Theoretical Component Limits Shown |
Storage Temperature Range | -67°F (-55°C) | 70°F (21°C) | 185°F (85°C) | Theoretical Component Limits Shown |
Operational Ambient Air Humidity | 0% | 50% | 70% | Non-Condensing Humidity Values Shown |
USB Module Power Consumption | N/A | N/A | N/A |
USB Modules are Powered by the USB Port Do Not Consume Device Current |
RS-232 Module Power Consumption | 10mA | 20mA |
|
|
Ethernet Module Power Consumption | 58mA | 82mA | 100mA | |
WiFi Bluetooth USB Module Power Consumption | 37mA | 50mA | 100mA | Up to 300 Foot Indoor Wireless Range, Unobstructed. Up to 50 Foot Range Through Walls |
900MHz Wireless Module Power Consumption | 13mA | 30mA | 50mA | Up to 1,000 Foot Indoor Wireless Range, up to 2 Mile Outdoor Wireless Range using Included Antennas. Up to 28 Miles Outdoor Wireless Range using High-Gain Antennas. |
KFX Wireless Key Fob | 11mA | 15mA | 25mA | Up to 200 Feet Outdoor Wireless Range using 1, 2, 3, 4, or 5 Button Key Fobs. Up to 700 Feet Outdoor Wireless Range using 8-Button Remotes |
AD8 Analog Input Usage Notice
Analog Inputs should not have a voltage present when powered down. Use a 220 Ohm current limiting resistor on each input to prevent damage to the controller if voltage will be present on the analog input when this controller is powered down. Do not exceed 0 to 5VDC on any analog input or the on-board CPU will be damaged. Most analog inputs include a 10K Pull Up/Down resistor to help keep the inputs quiet when not in use. This 10K resistor may slightly bias the readings of some sensors.LRR420_USB Accessories
Power Supply Available
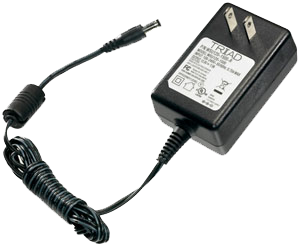
Click Here for More
Induction Suppression
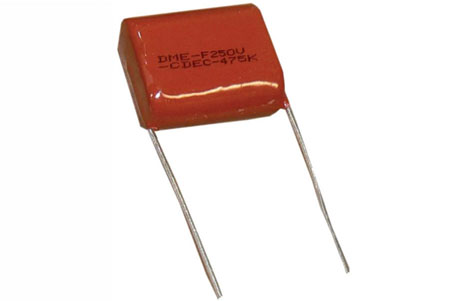
Base Station

Click for more on Base Station.
What Is Relay Logic?
Relay logic consists of relays wired together in a particular configuration to perform the desired switching operations. Relay Logic is all about wiring up Relays for Logical Switching applications. Get a printout of this page
Relay Logic
Relay Wiring Samples
This page demonstrates several simple ways to wire a relay or multiple relays for various applications. We use the example of switching a light but the light can be swapped for a gate control, security system, dry contact output and other devices. These examples show different ways to wire to a relay or multiple relays to produce a desired effect.Get a printout of this page
SPDT Wiring
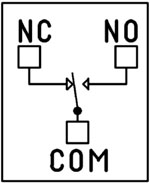
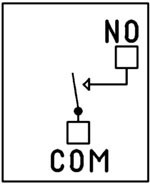
SPST Wiring
SPST Single Pole Single Throw Relays have two connections - Common and Normally Open. The Common (COM) is the moving part of the relay that comes in contact with the Normally Open (NO) when the coil to the relay is energized. The only SPST relay we sell on this site is the 30-Amp relays, The wiring examples below can be used with the 30-Amp relays as long as the example doesn't use the Normally Closed position.DPDT Wiring
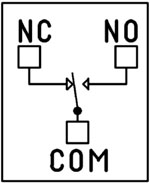
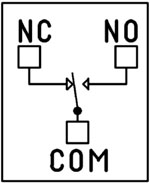
Relay Logic Examples
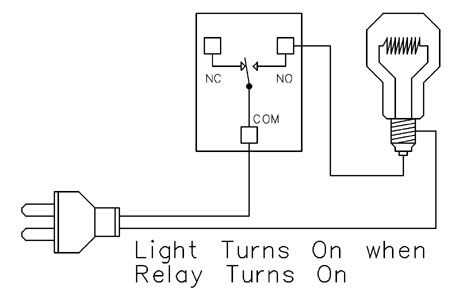
Example 1 - Simple Off/On
This example demonstrates how a relay can be used to activate a light bulb. When the relay turns on, the light comes on. Only one power wire is switched with this example using the COM (common) and NO (normally open) connections of a relay. This is the simplest of the examples, switching a light in this example or any device on when the relay is energized.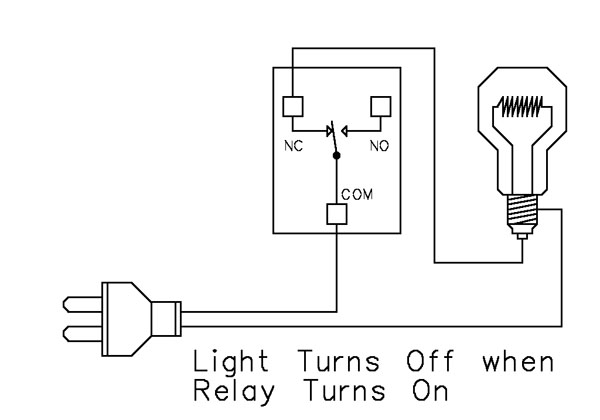
Example 2 - Simple On/Off
This example demonstrates how a relay can be used to turn a light bulb OFF. When the relay is energized the light turns off, when the relay is off the light will be ON. Only one power wire is switched in this sample using the COM (common) and NC (normally closed) connections of a relay. Not commonly used but great for applications where the device is on most of the time so the relay doesn't have to be energized to to keep the device on. Power cycling a device can be a typical use for this wiring, when the relay turns on the device is powered off.Example 3 - 2 Relays to Activate
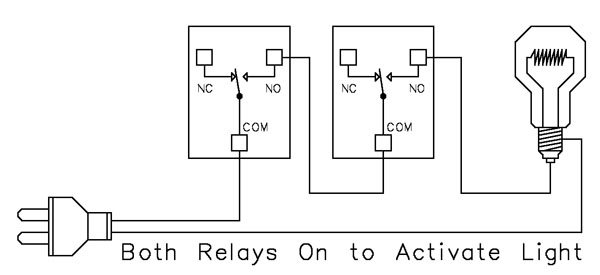
MirC/MirX Users: Two contact closure inputs in the sender board required to control a device. Use this wiring when you require two outputs to close before you switch the relay.
Example 4 - 3 Relays to Activate
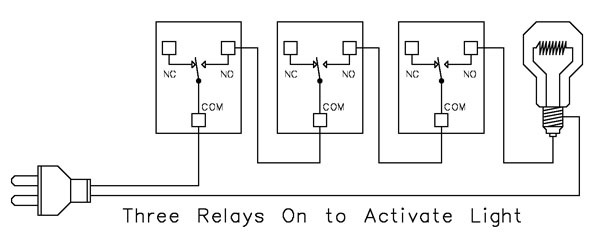
Example 5 - Override Function
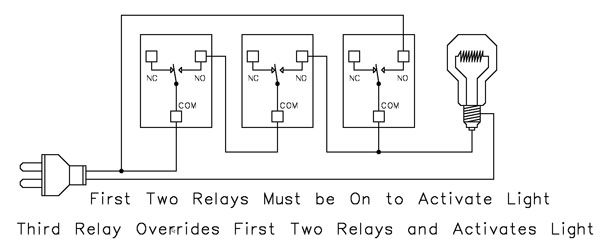
MirC/MirX Users: Add a manual button or switch to control the third relay to manually control the light if you have sensors that control the other relays.
Reactor Users: Add a manual button or switch to control the third relay to manually control the light if you have sensors that control the other relays.
Example 6 - Either Relay Activates
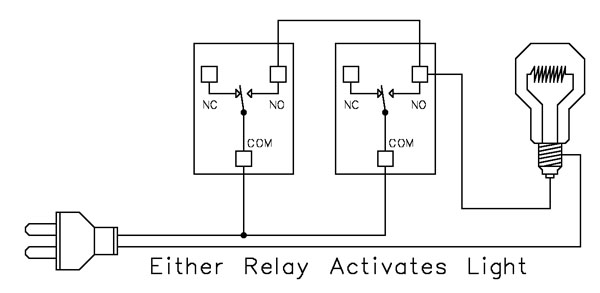
MirC/MirX Users: Two contact closure inputs in the sender board and either of the inputs can control one light or device.
Example 7 - 3-Way Switch
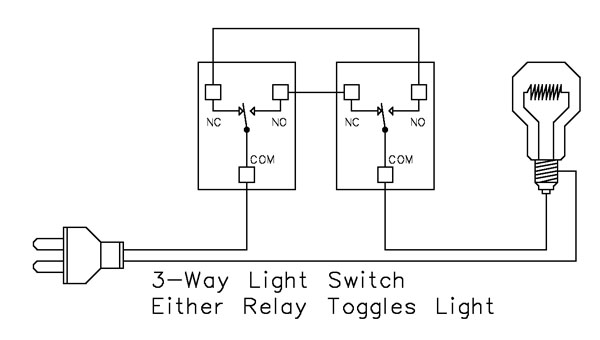
Example 8 - Motor Control
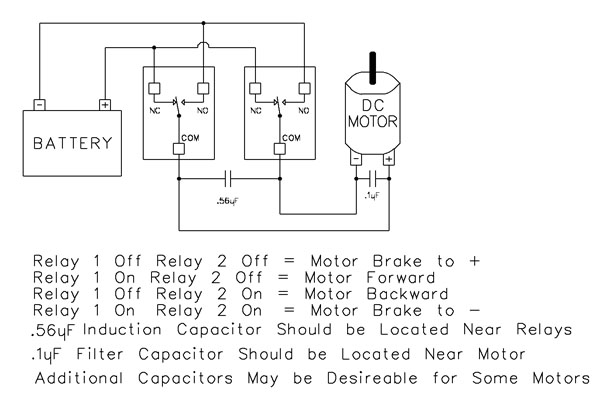
- Relay 1 Off Relay 2 Off = Motor Brake to +
- Relay 1 On Relay 2 Off = Motor Forward
- Relay 1 Off Relay 2 On = Motor Backward
- Relay 1 On Relay 2 On = Motor Brake to -
- Induction Capacitor Should Be located by relay
- Filter Capacitor Should be Located Near Motor
- Additional Capacitors May be Desirable for Some Motors