Time Activated Relay 1-Channel 30-Amp with USB Interface
TLR130_USB
Operates Without a Computer!
The TLR130_USB Time Activated Relay knows what time and day it is and will control relays according to your time schedule. USB Time Control connects directly to a USB port on your computer to upload your time schedule to the board using Base Station (a free download). Once uploaded the computer is no longer needed and the board will operate on it's own! Control gates at specific times of the day, activate security lighting, or control bells to indicate shift or classroom changes. Schedules can be save to your computer for easy upload when different schedules are needed!Schedule All the Events You Need!
The TLR130_USB can store up to one thousand time activated events! If your current time schedule software only allows you a limited amount of events for school bells or shift changes, you will have more than enough with this controller! Save schedules to your computer and easliy upload them to the board for different schedule options such as summer/winter schedules!
Time Activated Relay 1-Channel 30-Amp with USB Interface
TLR130_USB- OVERVIEW
- USB Interface
- Taralist Setup
- Features
- ProXR Expansion
- Power & More
- Relay Logic
- ACCESSORIES
- Data Sheets
USB Time Relay at a Glance
- 1 30-Amp Relay Installed
- Single Pole Single Throw (SPST) Relay
- Wire to Normally Open Position Only
- Wire Using 1/4" Quick Disconnect Terminal
- Temperature Rating -40° C to 85° C
- Expandable up to 256 Relay - Onboard USB Interface Module
- Plugs Directly into USB Port
- Use to Upload Time Schedule - Time Activated Relay w/Integrated Real Time Clock
- Control Relays on Your Time Schedule
- Board Operates Without a Computer
- Supports Daylight Savings Time
- Battery Backup in Case of Power Loss
FTDI Driver
The FT232RL mounts as a COM Port on your PC, Mac, or Linux computers when the appropriate drivers are installed from http://www.ftdichip.com/FTDrivers.htm. Also known as a VCP or Virtual COM Port, the FTDI series chips are second to none in quality, compatibility, Drivers, and reliability.
Taralist USB Configuration
USB Configuration
The time schedule must be configured using a computer and Base Station Software (a free download). Once configured, the board will operate without a computer. By choosing a USB version you will connect your computer to the board via a USB cable. This is the easiest and most popular way to connect to the Taralist Board. At any time, a computer may monitor the Taralist board, Trigger Events, Activate Relays, or Change schedules. A computer can take over a Taralist or a Taralist can operate autonomously (without a computer).Mounts as a COM Port
This Time Activated Relay connects to the USB port of your computer and will mount as a COM port on your PC. USB Drivers may be needed and links can be found in the USB Quick Start Guide. Windows 7, 8 & 10 users will automatically download and install the necessary drivers.ZUSB Modules
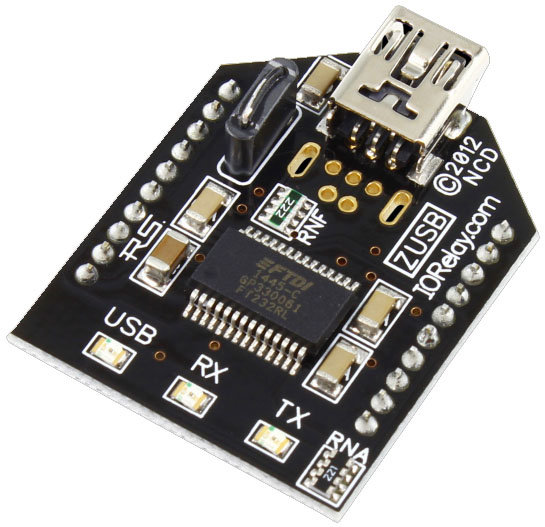
Take Manual Control of Taralist
At any time, a computer may monitor the Taralist Controller to read the status of the relays, activate relays, or change configuration settings using Base Station Software. This USB version will allow access to the board as long as it is still connected to the USB port of your computer. A computer can take over the Taralist or the Taralist can operate autonomously (without a computer). The Taralist Configuration Utility is part of Base Station software and this is a free download.Once Configured
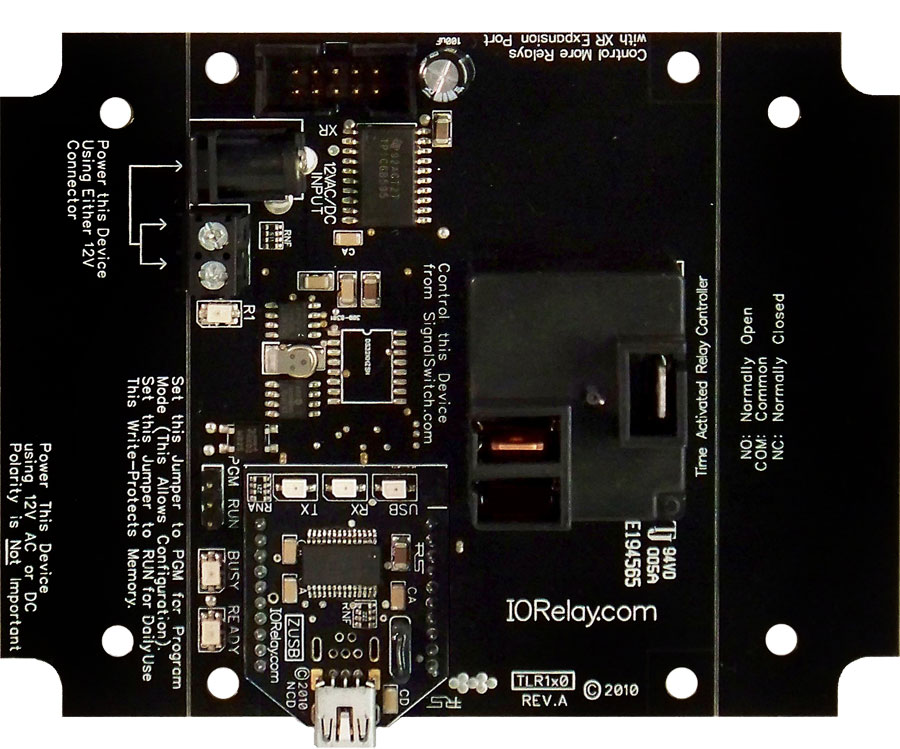
Controlling Relays
There are 2 possible ways to control the relays on a Taralist Series controller.- A Relay can be Directly Controlled by a time schedule.
- This Relay can be controlled from a computer through a USB connection. A computer can take control of any or all relays on a Taralist controller at any time. Once taken over, the Taralist logic will not be able to switch a relay. The computer MUST return control of the relay back to the Taralist Logic for standalone operation.
Who's Qualified to Use the Taralist Series?
Some computer skills required. The Taralist Relays do not require programming, simply configure the device with the included Base Station Software. While programming is not required and simple functions can be done rather easily with basic computer skills, complex events can be configured which will require some understanding and patience.Induction Capacitors
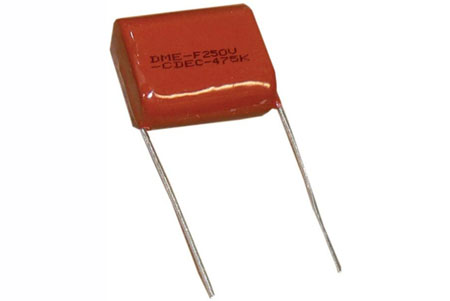
Base Station Software
Taralist boards are configured using the Free Base Station Software. The GUI interface makes it easy to configure simple automation tasks with a point and click interface! Configure time schedules and upload to the board and take manual control of relays. Download Base Station
Base Station Taralist Setup
Base Station Software
Base Station software works by communicating with your controller to identify the model and provides the appropriate graphical user interface for setting the time schedule and uploading it to the board. Base Station Software is used to configure and upload the time schedules to the Board and take manual control of the board to override the time schedule.Download Base Station
Integrated Real Time Clock
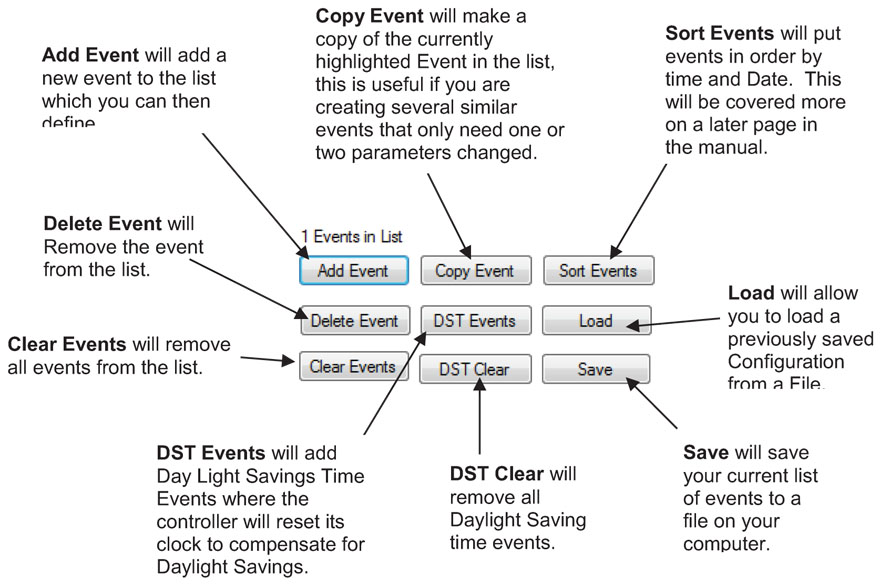
Time Schedule Events
Events are scheduled times when a relay or group of relays are turned on or off. They are defined by the user first by time: Year, Month, Day of Month, Day of week, Hour, Minute, and Second. You have the ability of switching relays on or off at very specific times! Activate relays only when the day is Monday, activate relays when the day is Monday and the Year is 2020, activate relays when the day is Monday, the year is 2020 at 9:44:21 AM. They are also defined by how they control the relays, whether they turn a relay or group of relays on or off. You can add up to 1000 Events to the list.Program Multiple Schedules
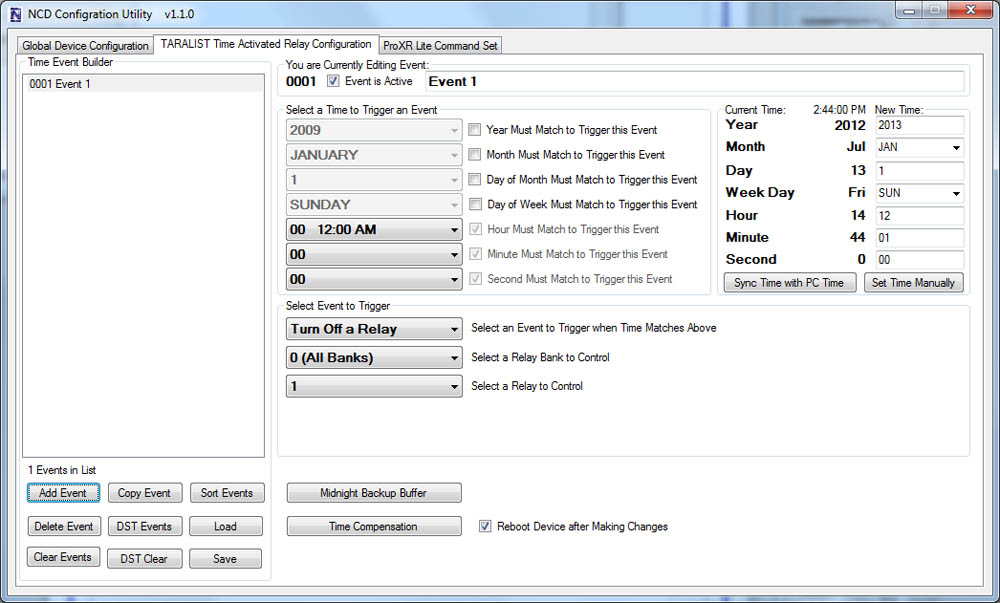
Daylight Savings Time is also supported, and is FULLY CUSTOMIZEABLE. As we all know, DST laws change periodically, but the Taralist series allow you to change the year and date of all DST events (we have programmed the US dates until 2030).
Save You Schedules
Taralist controllers allow you to build and save your time schedule as a file on your computer. Different schedules can be configured for different times of the year, for instance one for Summer School and one for the full school year. Upload the schedule you need for that part of the year. For users with multiple boards saved schedules can also be used to store the time schedule into each controller easily without re configuring.Clock Accuracy - Adjustable Time Compensation
Like most clocks, time drift is a reality and the Taralist controller will drift over time. The Taralist clock has some special features to help keep the time accurate. Time compensation functions are included that allow you to automatically adjust the clock forward or back (by up to 15 seconds) each day of the week. For instance, you may find the Taralist keeps better time if it automatically advances the clock 1 second each day of the week. Or you may find that you need to subtract 5 seconds from the clock 1 day per week. Adjustable time compensation will help keep your clock accurate (though it is always a good idea to check on the clock periodically).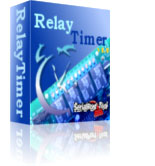
If your application requires your relay control to match a computer's time exactly we recommend using a computer controlled Relay and Relay Timer Software. The software can be installed on a computer or server and match the time exactly. We recommend this for school bells and shift change applications where matching a time clock is vital. Select a Wired or Wireless Relay under Relay Control from the top menu to select a board then add the Relay Timer Software at checkout.
Manual Control
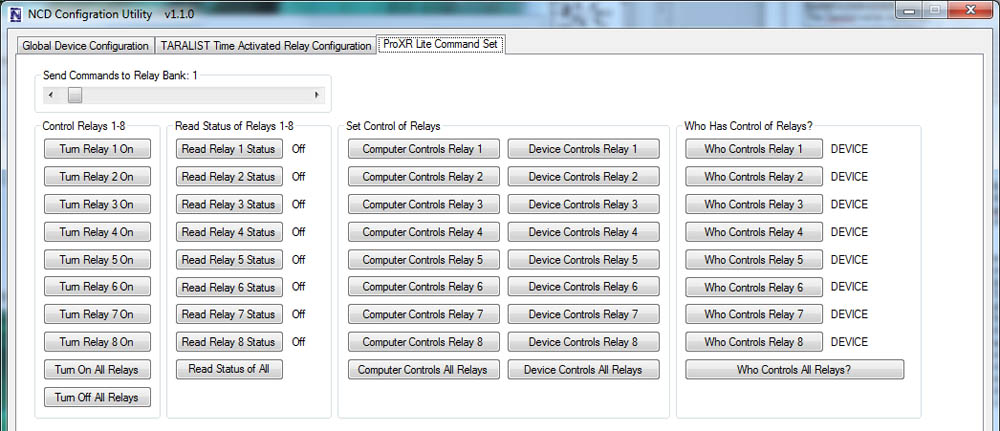
The interface elements shown at right allow a computer to take over control of any relay and force the relays to a On or Off state. You may also turn all relays on or off using the all relays on and all relays off buttons. You can also read the status of relays by clicking the Read Relay 1-8 Status. The Status of the relay will be shown to the right of the button. The slider at the top of the screen allows you to select with bank of relays these commands are directed to.
Power Loss Backup Buffer
The Midnight Backup Buffer is a special feature developed to help keep track of which relays should be activated in the event power is lost. Every night at midnight, the current status of all relays is stored in non-volatile memory. If power is lost, the Taralist will load the status of the relays from memory. Next, the Taralist will calculate all events from midnight to the current time to determine if any relays need to be activated or deactivated. Finally, the Taralist will refresh all relays and will be ready for normal operation.Program Up To 1000 Events
Up to 1000 timing events can be programed and uploaded to the board using Base Station Software, a free download. Once uploaded the board knows what day and time it is and can operate on it's own without a computer.
Download Base Station
Taralist Board Features
Time Activated Relay
We've looked at the interface and the configuration now let's take a look at the board design itself. The Taralist series controllers are machine manufactured for a highly accurate and reliable design. Fully tested before they leave the production facility each Taralist controller is ready to stand up to rigorous demands from heat, cold or vibration. The best test of all is the numerous boards in the field from customers all over the world in all sorts of conditions. Take it from us, these controllers will hold up!SPST Relay Installed
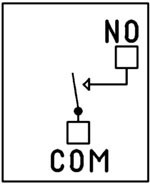
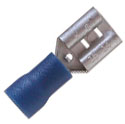
Powering the Board
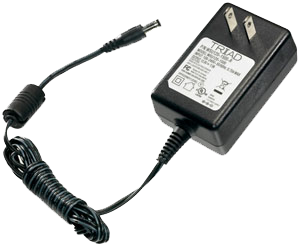
Aproximate Power Usage
- 100ma for logic of of the board to process commands
- 250ma for WiFi & wireless communications
- 80ma for each relay that is activated
Break-A-Way Tabs for a Smaller Design
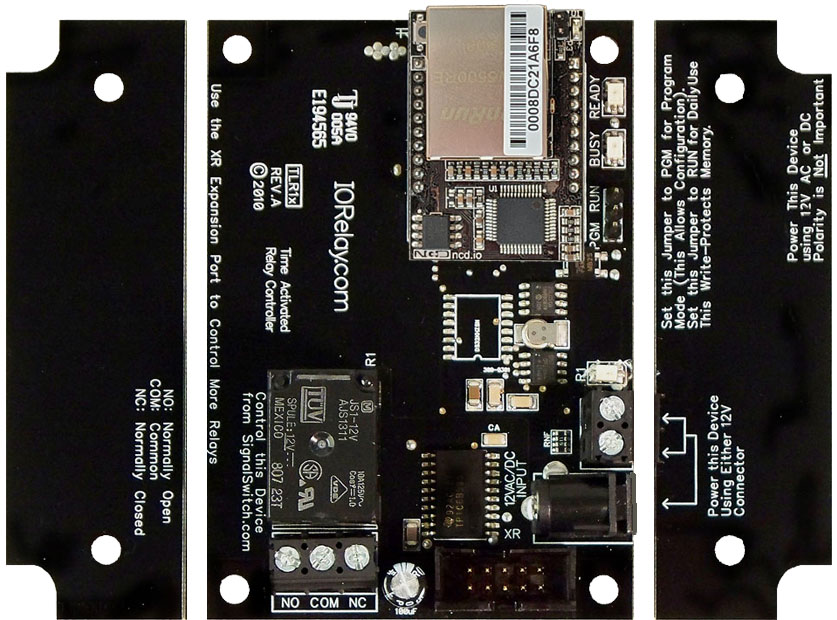
Add Relays as Your Needs Grow
Time Activated Relays are expandable up to 256 total relays. The controller is fitted with an XR Expansion Port where you can add expansion boards to this relay. The Expansion Boards get their logic from the main board and will require 12 VDC regulated power. Expansion boards do not need to be the same relay amperage as the main board or other expansion boards.2-Million Cycles
ProXR series controllers are designed for long life, you should expect to get years of service from your controller and literally 2-million cycles from the relays on board. With a 5-year warranty and a money back guarantee you have nothing to loose! Place your order now, while everything is in front of you.RoHS Compliant
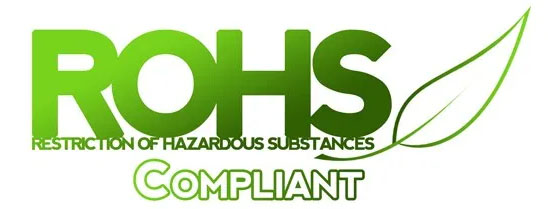
30-Day Warranty/Money Back Guarantee
Taralist series controllers are guaranteed against manufacturing and functionality defects for a full 30 days! Not to mention a 30-day money back guarantee! If for any reason you are not happy with a relay purchased from Relay Pros, simply return it within 30 days and we will give you your money back! Controllers that are damaged by our customers or have the Break-A-Way tabs removed will not of course be warranted under any circumstances.Shipping & Lead Time
The boards sold are brand new units shipped from our office conveniently located in Missouri. These boards are completely tested before they are released for shipping With so many boards on our site it is impossible to stock boards, please allow 3 to 5 days lead time for your order to ship. If you have any questions please feel free to call our office at 800-960-4287 or e-mail us at sales@relaypros.com.Time Activated Relay Is Here!

- User Friendly Software
- Point & Click Interface - No Programming Knowledge Required
- Override Time Schedule When Computer is Connected to Board
- Read Status of Relays in Base Station
- User Friendly Board Design
- Break-A-Way Tabs lets you decide the board's size
- Direct relay connections make connecting easy
ProXR Expansion Board
This Expansion Board plugs into the XR Expansion Port on any ProXR Board to add more relays. Expansion boards can be daisy chained together to add the relays needed.
The XR Expansion Port
Add Relays as Your Needs Grow
ProXR Controllers were built with relay expansion in mind. The XR Expansion Port is used to add banks of external relays to a ProXR or Taralist board equipped with a XR Expansion port. The ProXR and Taralist boards are fitted with an XR Expansion Port where you can add expansion boards. Expansion boards can be added until you reach 256 total relays. As you continue to chain expansion boards onto an XR expansion port, the total number of available relay banks will increase. Add expansion boards as needed in the future, whenever you require more relays simply order another expansion board.Linking XR Expansion Boards Together
XR Expansion Boards consist of a XR Input and XR Output Connector. Simply connect the XR Output of your ProXR Board to the XR Input located on the relay expansion board. Chaining more relays is easy. Simply connect the XR Output of your ProXR expansion board to the XR Input of your next expansion board. Mix and Match different relay types as your application requires. A 6″ expansion cable is included with the expansion board. It's important to keep the cabling as short as possible. Not all users will be able to expand to 256 total relays, as it all depends on the installation, the amount of electrical interference, and the overall cable length. For best compatibility, the total length of the ProXR controller and all of the expansions and cabling should not exceed 1 or 2 meters.Will Not Operate Independently
This Expansion Board gets it's commands from the main ProXR or Taralist board and will not operate independently. This board MUST be plugged into a ProXR or Taralist board to operate and will not function on it's own.Essential Power Requirements
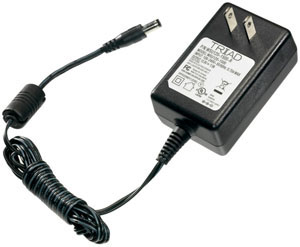
Maximum Relay Rating Notes
ProXR is capable of expanding to an absolute maximum of 256 Relays. In some cases, it may not be possible to control all 256 relays, particularly in applications where high noise levels may be involved. Experimentation may be required, as it is not possible for us to guarantee all users will be able to utilize all 256 relays in every application. Noise tends to accumulate when several expansions are connected together. For best results, the XR expansion cables must be as short as possible.SPST Relay Installed
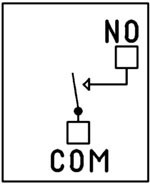
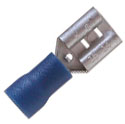
Mix & Match
Expansion boards do not need to be the same relay amperage as the main board or other expansion boards. Mix & match expansion board to get the exact amperage for your switching needs.2-Million Cycles
ProXR series controllers are designed for long life, you should expect to get years of service from your controller and literally 2-million cycles from the relays on board. With a 5-year warranty and a money back guarantee you have nothing to loose! Place your order now, while everything is in front of you.This Board is RoHS Compliant
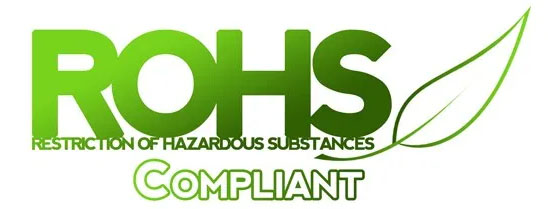
5-Year Warranty/Money Back Guarantee
ProXR Lite series controllers are guaranteed against manufacturing and functionality defects for a full 5 years! Not to mention a 30-day money back guarantee! If for any reason you are not happy with a relay purchased from Relay Pros, simply return it within 30 days and we will give you your money back! Controllers that are damaged by our customers will not of course be warranted under any circumstances.Shipping
The boards sold are brand new units shipped from our office conveniently located in Missouri. These boards are completely tested before they are released for shipping With so many boards on our site it is impossible to stock boards, please allow two to three days production time for your order to ship. If you have any questions please feel free to call our office at 800-960-4287 or e-mail us at sales@relaypros.com.Relay Expansion Videos
Building a Power Budget
The operating range of the board is between 9 & 14 VDC, any power outside this range and the board can become unreliable. Use the tables below to build a power budget for the board you have based on the module you have and the anticipated time the relay will be active.
Power & More
20/30 Amp Relay Board Specifications
This table covers all NCD boards with 20 or 30 amp relays installed. All ratings assume 12VDC operation at 70°F (21°C). Please note that most ratings are estimated and may be subject to periodic revision. Some ratings represent stock controller settings without performance enhancement optimizations. The estimated processing time can be impacted by background services and choice of commands. Standby power consumption assume no communications module is installed and no relays are active on the controller. Please add the power consumption of the activated relays and communications module to obtain a better estimation of power consumption.Specs of NCD SPDT Relay Boards | Minimum | Nominal | Maximum | Notes |
Operational Voltages | 10VDC | 12VDC | 15VDC | |
Standby Power Consumption | 35mA | 100mA | 200mA | No Active Relays, No Com Module |
Relay Power Consumption | 28mA | 35mA | 60mA | Consumption of Each Activated Relay |
Operational Temperature Range | -40°F (-40°C) | 70°F (21°C) | 185°F (85°C) | Theoretical Component Limits Shown |
Storage Temperature Range | -67°F (-55°C) | 70°F (21°C) | 185°F (85°C) |
Theoretical Component Limits Shown |
Operational Ambient Air Humidity | 0% | 50% | 70% | Non-Condensing Humidity Values Shown |
Relay Activation Time | 15ms | Needs Further Validation | ||
Relay Deactivation Time | 10mS | Needs Further Validation | ||
Operational Life Mechanical | 10,000,000 | Component Operation Rating | ||
Operational Life Electrical | 100,000 | Component Rating at Maximum Load |
Communication Module Specifications
This table covers all NCD Communication Modules. While NCD communication modules operate at 3.3VDC, the ratings below highlight the effect they will have on the master controller operating at 12VDC at 70°F (21°C). Maximum ratings should be used for power budget planning purposes and may reflect short term absolute maximum peak current consumption. Some ratings are estimated and subject to periodic revision.Specs of NCD Communication Modules | Minimum | Nominal | Maximum | Notes |
Operational Temperature Range | -40°F (-40°C) | 70°F (21°C) | 185°F (85°C) | Theoretical Component Limits Shown |
Storage Temperature Range | -67°F (-55°C) | 70°F (21°C) | 185°F (85°C) | Theoretical Component Limits Shown |
Operational Ambient Air Humidity | 0% | 50% | 70% | Non-Condensing Humidity Values Shown |
USB Module Power Consumption | N/A | N/A | N/A |
USB Modules are Powered by the USB Port Do Not Consume Device Current |
RS-232 Module Power Consumption | 10mA | 20mA |
|
|
Ethernet Module Power Consumption | 58mA | 82mA | 100mA | |
WiFi Bluetooth USB Module Power Consumption | 37mA | 50mA | 100mA | Up to 300 Foot Indoor Wireless Range, Unobstructed. Up to 50 Foot Range Through Walls |
900MHz Wireless Module Power Consumption | 13mA | 30mA | 50mA | Up to 1,000 Foot Indoor Wireless Range, up to 2 Mile Outdoor Wireless Range using Included Antennas. Up to 28 Miles Outdoor Wireless Range using High-Gain Antennas. |
KFX Wireless Key Fob | 11mA | 15mA | 25mA | Up to 200 Feet Outdoor Wireless Range using 1, 2, 3, 4, or 5 Button Key Fobs. Up to 700 Feet Outdoor Wireless Range using 8-Button Remotes |
AD8 Analog Input Usage Notice
Analog Inputs should not have a voltage present when powered down. Use a 220 Ohm current limiting resistor on each input to prevent damage to the controller if voltage will be present on the analog input when this controller is powered down. Do not exceed 0 to 5VDC on any analog input or the on-board CPU will be damaged. Most analog inputs include a 10K Pull Up/Down resistor to help keep the inputs quiet when not in use. This 10K resistor may slightly bias the readings of some sensors.Accessories
Power Supply Available
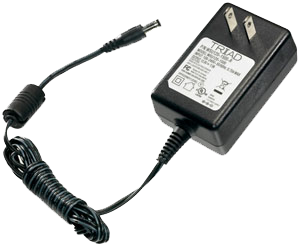
Click Here for More
Enclosure Available

GFL Spec Sheet
CAD Drawing: GFL CAD Drawing
3D Model: GFL_3D
Quick Disconnect Terminal
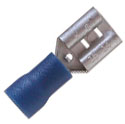
Induction Suppression
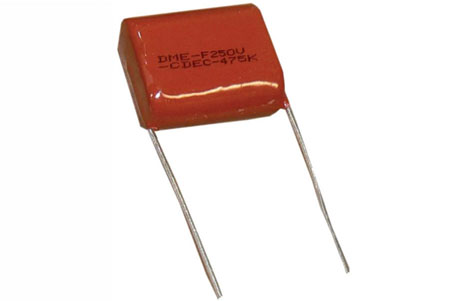
Base Station

Click for more on Base Station.
What Is Relay Logic?
Relay logic consists of relays wired together in a particular configuration to perform the desired switching operations. Relay Logic is all about wiring up Relays for Logical Switching applications. Get a printout of this page
Relay Logic
Relay Wiring Samples
This page demonstrates several simple ways to wire a relay or multiple relays for various applications. We use the example of switching a light but the light can be swapped for a gate control, security system, dry contact output and other devices. These examples show different ways to wire to a relay or multiple relays to produce a desired effect.Get a printout of this page
SPDT Wiring
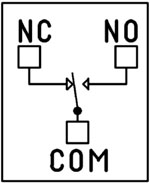
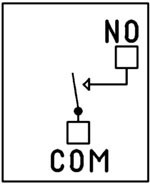
SPST Wiring
SPST Single Pole Single Throw Relays have two connections - Common and Normally Open. The Common (COM) is the moving part of the relay that comes in contact with the Normally Open (NO) when the coil to the relay is energized. The only SPST relay we sell on this site is the 30-Amp relays, The wiring examples below can be used with the 30-Amp relays as long as the example doesn't use the Normally Closed position.DPDT Wiring
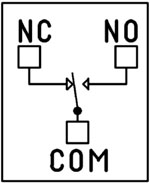
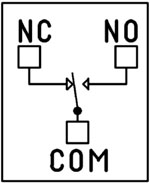
Relay Logic Examples
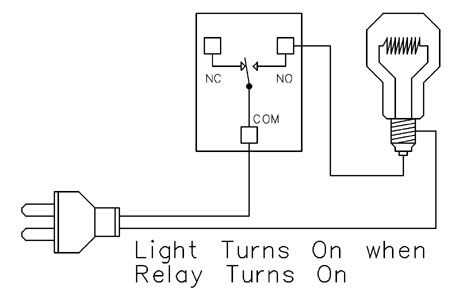
Example 1 - Simple Off/On
This example demonstrates how a relay can be used to activate a light bulb. When the relay turns on, the light comes on. Only one power wire is switched with this example using the COM (common) and NO (normally open) connections of a relay. This is the simplest of the examples, switching a light in this example or any device on when the relay is energized.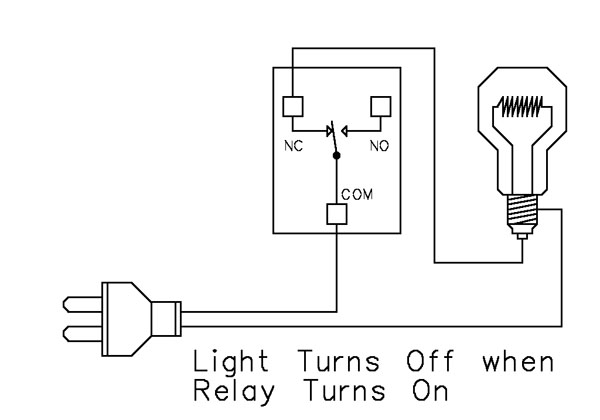
Example 2 - Simple On/Off
This example demonstrates how a relay can be used to turn a light bulb OFF. When the relay is energized the light turns off, when the relay is off the light will be ON. Only one power wire is switched in this sample using the COM (common) and NC (normally closed) connections of a relay. Not commonly used but great for applications where the device is on most of the time so the relay doesn't have to be energized to to keep the device on. Power cycling a device can be a typical use for this wiring, when the relay turns on the device is powered off.Example 3 - 2 Relays to Activate
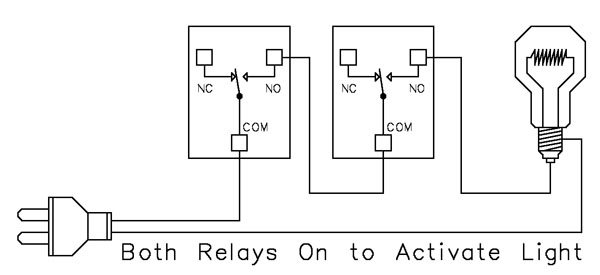
MirC/MirX Users: Two contact closure inputs in the sender board required to control a device. Use this wiring when you require two outputs to close before you switch the relay.
Example 4 - 3 Relays to Activate
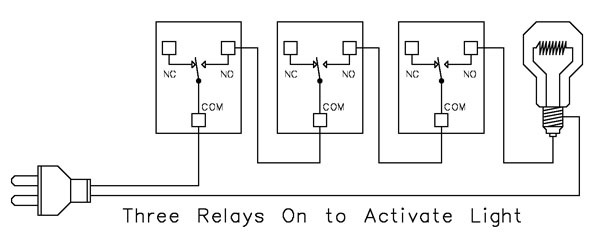
Example 5 - Override Function
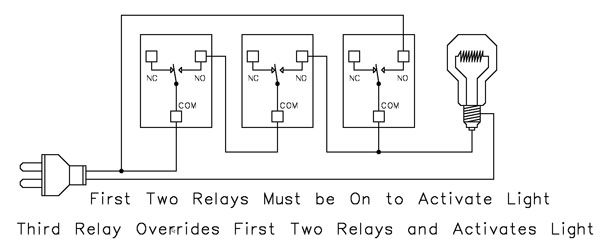
MirC/MirX Users: Add a manual button or switch to control the third relay to manually control the light if you have sensors that control the other relays.
Reactor Users: Add a manual button or switch to control the third relay to manually control the light if you have sensors that control the other relays.
Example 6 - Either Relay Activates
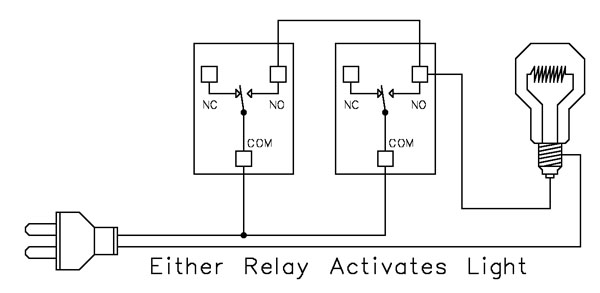
MirC/MirX Users: Two contact closure inputs in the sender board and either of the inputs can control one light or device.
Example 7 - 3-Way Switch
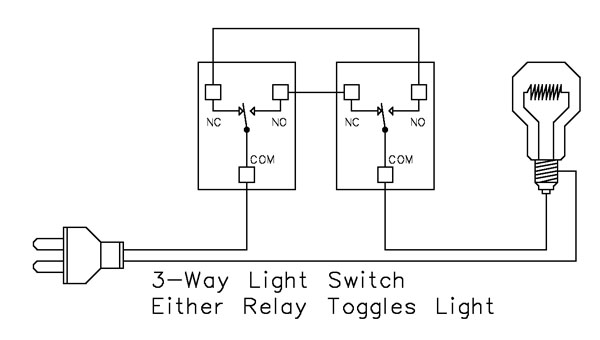
Example 8 - Motor Control
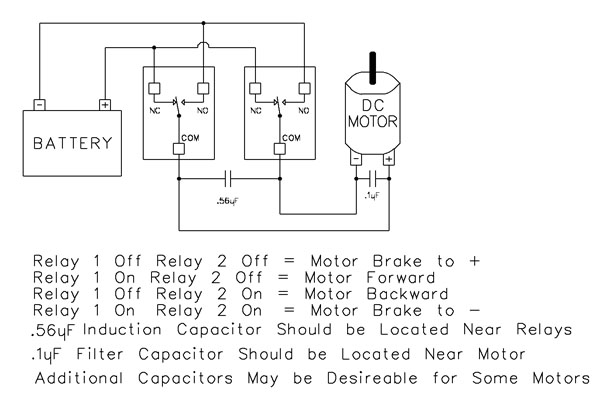
- Relay 1 Off Relay 2 Off = Motor Brake to +
- Relay 1 On Relay 2 Off = Motor Forward
- Relay 1 Off Relay 2 On = Motor Backward
- Relay 1 On Relay 2 On = Motor Brake to -
- Induction Capacitor Should Be located by relay
- Filter Capacitor Should be Located Near Motor
- Additional Capacitors May be Desirable for Some Motors